What are the Manufacturing Processes of the Latest Precision Resistors?
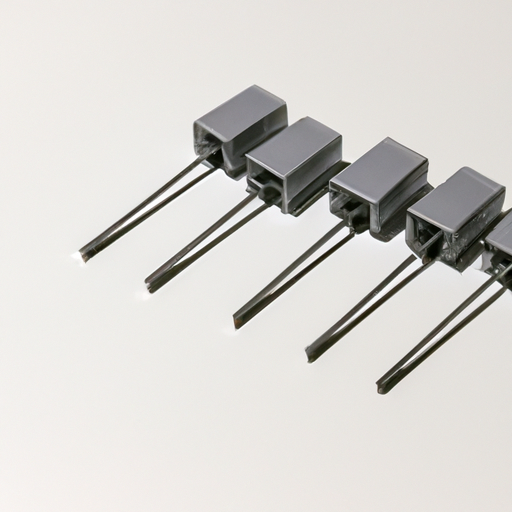
I. Introduction
Precision resistors are critical components in modern electronics, providing accurate resistance values essential for circuit functionality. These resistors are designed to maintain their resistance under varying conditions, ensuring reliability and performance in applications ranging from consumer electronics to aerospace systems. As technology advances, the demand for precision resistors has increased, leading to innovations in their manufacturing processes. This blog post will explore the various types of precision resistors, the key manufacturing processes involved, quality control measures, and the latest innovations in the field.
II. Types of Precision Resistors
A. Thin Film Resistors
Thin film resistors are made by depositing a thin layer of resistive material onto a substrate. They are known for their high accuracy, low temperature coefficient, and excellent stability. Common applications include precision measurement instruments and high-frequency circuits. The thin film technology allows for tight tolerances, making them ideal for applications where precision is paramount.
B. Thick Film Resistors
Thick film resistors are created by printing a paste of resistive material onto a substrate and then firing it at high temperatures. These resistors are more robust than thin film types and can handle higher power levels. They are widely used in consumer electronics, automotive applications, and industrial equipment. While they may not offer the same level of precision as thin film resistors, advancements in thick film technology have significantly improved their performance.
C. Wirewound Resistors
Wirewound resistors are constructed by winding a metal wire around a core. This design allows for high power ratings and excellent heat dissipation. They are commonly used in applications requiring high precision and stability, such as in power supplies and audio equipment. Wirewound resistors can be manufactured to very tight tolerances, making them suitable for precision applications.
D. Foil Resistors
Foil resistors are made from a thin foil of resistive material that is cut and shaped to create the desired resistance. They offer exceptional stability and low temperature coefficients, making them ideal for precision applications. Foil resistors are often used in high-end measurement equipment and precision analog circuits due to their superior performance characteristics.
III. Key Manufacturing Processes
A. Material Selection
The manufacturing of precision resistors begins with careful material selection. The choice of conductive materials, such as metal films, carbon, or metal oxides, directly impacts the resistor's performance. Substrate materials, including ceramics and glass, are also critical, as they provide the necessary support and thermal stability.
B. Thin Film Deposition
Thin film resistors are produced through various deposition techniques, including:
1. **Sputtering**: This process involves bombarding a target material with ions, causing atoms to be ejected and deposited onto the substrate. Sputtering allows for precise control over the thickness and composition of the film.
2. **Chemical Vapor Deposition (CVD)**: In CVD, gaseous precursors react on the substrate surface to form a solid film. This method is known for producing high-quality films with excellent uniformity.
3. **Physical Vapor Deposition (PVD)**: PVD techniques, such as evaporation, involve vaporizing a solid material in a vacuum and allowing it to condense on the substrate. This method is widely used for creating thin films with specific electrical properties.
C. Thick Film Printing
Thick film resistors are manufactured using a screen printing process, where a paste containing conductive materials is printed onto a substrate. Key steps include:
1. **Screen Printing Process**: A stencil is used to apply the resistive paste onto the substrate. The paste is then cured at high temperatures to form a solid layer.
2. **Ink Formulation and Composition**: The formulation of the ink is crucial for achieving the desired resistance values and stability. Manufacturers carefully select the components to ensure optimal performance.
D. Wirewound Construction
The construction of wirewound resistors involves several steps:
1. **Wire Selection and Winding Techniques**: High-quality metal wire, often made of nickel-chromium or copper-nickel alloys, is selected for its resistive properties. The wire is then wound around a ceramic or fiberglass core, with the number of turns determining the resistance value.
2. **Insulation and Encapsulation**: After winding, the resistor is insulated to prevent short circuits and encapsulated to protect it from environmental factors. This ensures durability and reliability in various applications.
E. Foil Resistor Fabrication
Foil resistors are fabricated through a series of precise steps:
1. **Foil Cutting and Shaping**: A thin foil of resistive material is cut into the desired shape and size. The cutting process must be precise to maintain the resistor's specifications.
2. **Bonding Techniques**: The foil is bonded to the substrate using adhesives or soldering techniques. This step is critical for ensuring good electrical contact and mechanical stability.
IV. Quality Control and Testing
A. Importance of Quality Control in Precision Resistors
Quality control is paramount in the manufacturing of precision resistors. Even minor deviations in resistance values can lead to significant performance issues in electronic circuits. Manufacturers implement rigorous quality control measures to ensure that each resistor meets the specified tolerances and performance criteria.
B. Testing Methods
Several testing methods are employed to verify the performance of precision resistors:
1. **Resistance Measurement**: Automated systems measure the resistance of each resistor to ensure it falls within the specified tolerance range.
2. **Temperature Coefficient Testing**: This test evaluates how the resistance changes with temperature, providing insight into the resistor's stability under varying conditions.
3. **Long-term Stability Tests**: Resistors are subjected to prolonged stress tests to assess their performance over time. This helps identify any potential drift in resistance values.
C. Certification and Standards
Manufacturers adhere to various certification and standards, such as ISO and RoHS, to ensure product quality and compliance with environmental regulations. These certifications provide assurance to customers regarding the reliability and safety of the resistors.
V. Innovations in Precision Resistor Manufacturing
A. Advances in Materials Science
Recent advancements in materials science have led to the development of new conductive materials that offer improved performance characteristics. These materials enhance the stability and accuracy of precision resistors, making them suitable for even more demanding applications.
B. Automation and Robotics in Manufacturing
The integration of automation and robotics in the manufacturing process has significantly improved efficiency and precision. Automated systems can perform tasks such as material handling, assembly, and testing with high accuracy, reducing the risk of human error and increasing production rates.
C. Environmental Considerations and Sustainability
As the electronics industry becomes more environmentally conscious, manufacturers are exploring sustainable practices in resistor production. This includes using eco-friendly materials, reducing waste, and implementing energy-efficient manufacturing processes.
VI. Conclusion
In summary, precision resistors play a vital role in modern electronics, and their manufacturing processes have evolved significantly to meet the demands of advanced technology. From material selection to innovative manufacturing techniques, each step is crucial in ensuring the performance and reliability of these components. As we look to the future, advancements in materials science, automation, and sustainability will continue to shape the landscape of precision resistor manufacturing, further enhancing their role in advancing technology.
VII. References
1. Academic journals on materials science and electronics.
2. Industry reports on precision resistor manufacturing trends.
3. Manufacturer specifications and guidelines for precision resistors.
This comprehensive overview of the manufacturing processes of the latest precision resistors highlights the complexity and importance of these components in the electronics industry. As technology continues to advance, precision resistors will remain essential in ensuring the reliability and performance of electronic devices.
What are the Manufacturing Processes of the Latest Precision Resistors?
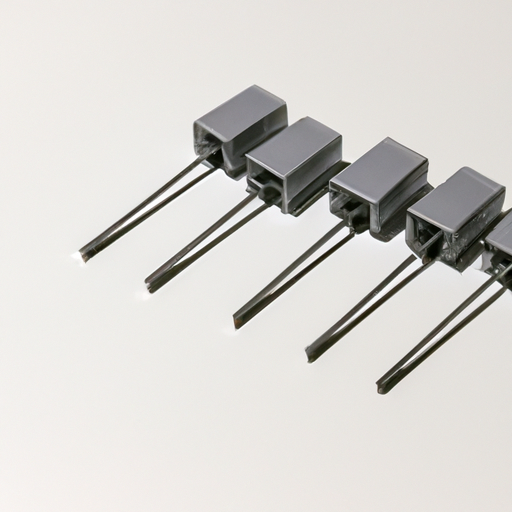
I. Introduction
Precision resistors are critical components in modern electronics, providing accurate resistance values essential for circuit functionality. These resistors are designed to maintain their resistance under varying conditions, ensuring reliability and performance in applications ranging from consumer electronics to aerospace systems. As technology advances, the demand for precision resistors has increased, leading to innovations in their manufacturing processes. This blog post will explore the various types of precision resistors, the key manufacturing processes involved, quality control measures, and the latest innovations in the field.
II. Types of Precision Resistors
A. Thin Film Resistors
Thin film resistors are made by depositing a thin layer of resistive material onto a substrate. They are known for their high accuracy, low temperature coefficient, and excellent stability. Common applications include precision measurement instruments and high-frequency circuits. The thin film technology allows for tight tolerances, making them ideal for applications where precision is paramount.
B. Thick Film Resistors
Thick film resistors are created by printing a paste of resistive material onto a substrate and then firing it at high temperatures. These resistors are more robust than thin film types and can handle higher power levels. They are widely used in consumer electronics, automotive applications, and industrial equipment. While they may not offer the same level of precision as thin film resistors, advancements in thick film technology have significantly improved their performance.
C. Wirewound Resistors
Wirewound resistors are constructed by winding a metal wire around a core. This design allows for high power ratings and excellent heat dissipation. They are commonly used in applications requiring high precision and stability, such as in power supplies and audio equipment. Wirewound resistors can be manufactured to very tight tolerances, making them suitable for precision applications.
D. Foil Resistors
Foil resistors are made from a thin foil of resistive material that is cut and shaped to create the desired resistance. They offer exceptional stability and low temperature coefficients, making them ideal for precision applications. Foil resistors are often used in high-end measurement equipment and precision analog circuits due to their superior performance characteristics.
III. Key Manufacturing Processes
A. Material Selection
The manufacturing of precision resistors begins with careful material selection. The choice of conductive materials, such as metal films, carbon, or metal oxides, directly impacts the resistor's performance. Substrate materials, including ceramics and glass, are also critical, as they provide the necessary support and thermal stability.
B. Thin Film Deposition
Thin film resistors are produced through various deposition techniques, including:
1. **Sputtering**: This process involves bombarding a target material with ions, causing atoms to be ejected and deposited onto the substrate. Sputtering allows for precise control over the thickness and composition of the film.
2. **Chemical Vapor Deposition (CVD)**: In CVD, gaseous precursors react on the substrate surface to form a solid film. This method is known for producing high-quality films with excellent uniformity.
3. **Physical Vapor Deposition (PVD)**: PVD techniques, such as evaporation, involve vaporizing a solid material in a vacuum and allowing it to condense on the substrate. This method is widely used for creating thin films with specific electrical properties.
C. Thick Film Printing
Thick film resistors are manufactured using a screen printing process, where a paste containing conductive materials is printed onto a substrate. Key steps include:
1. **Screen Printing Process**: A stencil is used to apply the resistive paste onto the substrate. The paste is then cured at high temperatures to form a solid layer.
2. **Ink Formulation and Composition**: The formulation of the ink is crucial for achieving the desired resistance values and stability. Manufacturers carefully select the components to ensure optimal performance.
D. Wirewound Construction
The construction of wirewound resistors involves several steps:
1. **Wire Selection and Winding Techniques**: High-quality metal wire, often made of nickel-chromium or copper-nickel alloys, is selected for its resistive properties. The wire is then wound around a ceramic or fiberglass core, with the number of turns determining the resistance value.
2. **Insulation and Encapsulation**: After winding, the resistor is insulated to prevent short circuits and encapsulated to protect it from environmental factors. This ensures durability and reliability in various applications.
E. Foil Resistor Fabrication
Foil resistors are fabricated through a series of precise steps:
1. **Foil Cutting and Shaping**: A thin foil of resistive material is cut into the desired shape and size. The cutting process must be precise to maintain the resistor's specifications.
2. **Bonding Techniques**: The foil is bonded to the substrate using adhesives or soldering techniques. This step is critical for ensuring good electrical contact and mechanical stability.
IV. Quality Control and Testing
A. Importance of Quality Control in Precision Resistors
Quality control is paramount in the manufacturing of precision resistors. Even minor deviations in resistance values can lead to significant performance issues in electronic circuits. Manufacturers implement rigorous quality control measures to ensure that each resistor meets the specified tolerances and performance criteria.
B. Testing Methods
Several testing methods are employed to verify the performance of precision resistors:
1. **Resistance Measurement**: Automated systems measure the resistance of each resistor to ensure it falls within the specified tolerance range.
2. **Temperature Coefficient Testing**: This test evaluates how the resistance changes with temperature, providing insight into the resistor's stability under varying conditions.
3. **Long-term Stability Tests**: Resistors are subjected to prolonged stress tests to assess their performance over time. This helps identify any potential drift in resistance values.
C. Certification and Standards
Manufacturers adhere to various certification and standards, such as ISO and RoHS, to ensure product quality and compliance with environmental regulations. These certifications provide assurance to customers regarding the reliability and safety of the resistors.
V. Innovations in Precision Resistor Manufacturing
A. Advances in Materials Science
Recent advancements in materials science have led to the development of new conductive materials that offer improved performance characteristics. These materials enhance the stability and accuracy of precision resistors, making them suitable for even more demanding applications.
B. Automation and Robotics in Manufacturing
The integration of automation and robotics in the manufacturing process has significantly improved efficiency and precision. Automated systems can perform tasks such as material handling, assembly, and testing with high accuracy, reducing the risk of human error and increasing production rates.
C. Environmental Considerations and Sustainability
As the electronics industry becomes more environmentally conscious, manufacturers are exploring sustainable practices in resistor production. This includes using eco-friendly materials, reducing waste, and implementing energy-efficient manufacturing processes.
VI. Conclusion
In summary, precision resistors play a vital role in modern electronics, and their manufacturing processes have evolved significantly to meet the demands of advanced technology. From material selection to innovative manufacturing techniques, each step is crucial in ensuring the performance and reliability of these components. As we look to the future, advancements in materials science, automation, and sustainability will continue to shape the landscape of precision resistor manufacturing, further enhancing their role in advancing technology.
VII. References
1. Academic journals on materials science and electronics.
2. Industry reports on precision resistor manufacturing trends.
3. Manufacturer specifications and guidelines for precision resistors.
This comprehensive overview of the manufacturing processes of the latest precision resistors highlights the complexity and importance of these components in the electronics industry. As technology continues to advance, precision resistors will remain essential in ensuring the reliability and performance of electronic devices.