What is the Mainstream Wirewound Resistor Production Process?
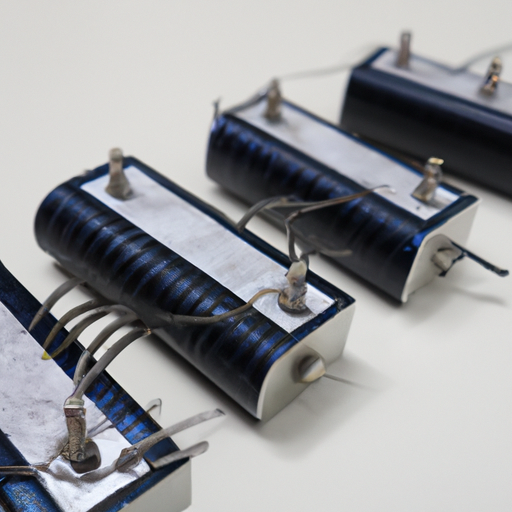
I. Introduction
Wirewound resistors are a type of resistor that is constructed by winding a metal wire around a core, typically made of ceramic or another insulating material. These resistors are known for their high precision, stability, and ability to handle high power levels, making them essential components in various electronic applications, from consumer electronics to industrial machinery. Understanding the production process of wirewound resistors is crucial for manufacturers and engineers alike, as it ensures the quality and reliability of these components. This blog post will delve into the materials, design specifications, production techniques, quality control measures, and future trends in the wirewound resistor industry.
II. Materials Used in Wirewound Resistors
A. Types of Wire Materials
The choice of wire material is critical in determining the performance characteristics of wirewound resistors. The most commonly used materials include:
1. **Nickel-chromium (NiCr)**: This alloy is favored for its excellent temperature stability and resistance to oxidation, making it suitable for high-temperature applications.
2. **Copper-nickel (CuNi)**: Known for its good conductivity and lower cost, CuNi is often used in applications where high precision is not as critical.
3. **Other alloys**: Various other alloys may be used depending on specific requirements, including resistance to corrosion and thermal stability.
B. Insulating Materials
Insulation is vital to prevent short circuits and ensure the resistor functions correctly. Common insulating materials include:
1. **Ceramic substrates**: These are often used for their high thermal stability and electrical insulation properties.
2. **Epoxy resins**: These materials provide good insulation and are often used in conjunction with ceramic substrates for added durability.
C. Coating Materials
Coatings serve both protective and functional purposes:
1. **Protective coatings**: These coatings protect the resistor from environmental factors such as moisture and dust.
2. **Color coding for identification**: Resistors are often color-coded to indicate their resistance values and tolerances, which is essential for easy identification during assembly and maintenance.
III. Design and Specifications
A. Determining Resistance Values
The resistance value of a wirewound resistor is determined by the length, cross-sectional area, and resistivity of the wire used. Engineers must carefully calculate these parameters to meet specific application requirements.
B. Power Rating Considerations
Power rating is a critical specification that indicates how much power a resistor can dissipate without overheating. This is influenced by the wire material, size, and insulation used.
C. Tolerance Levels
Tolerance levels indicate how much the actual resistance can vary from the specified value. High-precision applications may require resistors with tighter tolerances.
D. Size and Form Factor
The physical size and shape of the resistor are also important, as they must fit within the design constraints of the electronic device in which they will be used.
IV. The Production Process
A. Wire Preparation
1. **Wire drawing and annealing**: The production process begins with wire drawing, where metal is pulled through a die to achieve the desired diameter. Annealing follows to relieve stress and improve ductility.
2. **Cutting to specified lengths**: Once the wire is prepared, it is cut to the lengths required for the specific resistor design.
B. Winding the Wire
1. **Manual vs. automated winding**: Depending on the production scale, wire can be wound manually or using automated machines. Automated winding is more common in large-scale production due to its efficiency and consistency.
2. **Types of winding techniques**: Various winding techniques, such as helical or layered winding, can be employed based on the desired resistance and power rating.
C. Insulation Application
1. **Insulating the wire**: After winding, the wire is insulated to prevent electrical shorts. This can involve applying a thin layer of insulating material directly onto the wire.
2. **Application of ceramic or epoxy coatings**: The wound resistor is then coated with ceramic or epoxy to provide additional insulation and protection.
D. Sintering and Curing
1. **Sintering process for ceramic substrates**: If ceramic substrates are used, they undergo a sintering process where they are heated to a temperature that allows the particles to fuse together, enhancing their strength and insulating properties.
2. **Curing of epoxy coatings**: Epoxy coatings are cured through a chemical reaction that hardens the material, providing a durable protective layer.
E. Trimming and Testing
1. **Trimming to achieve precise resistance values**: After curing, the resistors are trimmed to achieve the exact resistance values specified in the design.
2. **Electrical testing for quality assurance**: Each resistor undergoes rigorous electrical testing to ensure it meets the required specifications and tolerances.
V. Quality Control Measures
A. In-process Inspections
Throughout the production process, in-process inspections are conducted to identify any defects or deviations from specifications. This includes checking wire diameter, winding consistency, and insulation integrity.
B. Final Testing Procedures
Once production is complete, final testing procedures are implemented to verify the performance of each resistor. This includes measuring resistance, power rating, and tolerance levels.
C. Compliance with Industry Standards
Manufacturers must ensure that their products comply with industry standards such as ISO and RoHS, which govern quality and environmental safety.
VI. Packaging and Distribution
A. Packaging Methods
Wirewound resistors are packaged in a manner that protects them during transportation and storage. This may involve anti-static bags, bubble wrap, or custom packaging solutions.
B. Labeling and Documentation
Each package is labeled with essential information, including resistance values, tolerances, and manufacturer details. Documentation may also include test results and compliance certifications.
C. Distribution Channels
Resistors are distributed through various channels, including direct sales to manufacturers, electronic component distributors, and online marketplaces.
VII. Challenges in Wirewound Resistor Production
A. Material Sourcing and Cost Fluctuations
The cost and availability of raw materials can fluctuate due to market conditions, impacting production costs and timelines.
B. Technological Advancements and Automation
While automation improves efficiency, it also requires manufacturers to invest in new technologies and training for their workforce.
C. Environmental Considerations and Sustainability
Manufacturers are increasingly focused on sustainability, seeking ways to reduce waste and energy consumption in the production process.
VIII. Future Trends in Wirewound Resistor Production
A. Innovations in Materials and Design
Research into new materials and designs is ongoing, with the aim of improving performance and reducing costs. This includes exploring alternative alloys and advanced insulation techniques.
B. Impact of Digitalization and Industry 4.0
The integration of digital technologies and Industry 4.0 principles is transforming production processes, enabling real-time monitoring and data analysis to enhance efficiency and quality.
C. Market Demand and Evolving Applications
As technology advances, the demand for high-precision wirewound resistors is expected to grow, particularly in sectors such as automotive, telecommunications, and renewable energy.
IX. Conclusion
The production process of wirewound resistors is a complex and meticulous endeavor that requires careful consideration of materials, design specifications, and quality control measures. As the demand for high-quality electronic components continues to rise, manufacturers must adapt to new challenges and embrace innovations to remain competitive. The future of the wirewound resistor industry looks promising, with advancements in materials and technology paving the way for enhanced performance and sustainability.
X. References
- Academic journals on electronic components and materials science.
- Industry reports on resistor manufacturing trends and market analysis.
- Manufacturer guidelines and specifications for wirewound resistors.
This comprehensive overview of the wirewound resistor production process highlights the intricacies involved in creating these essential electronic components, emphasizing the importance of quality and precision in manufacturing.
What is the Mainstream Wirewound Resistor Production Process?
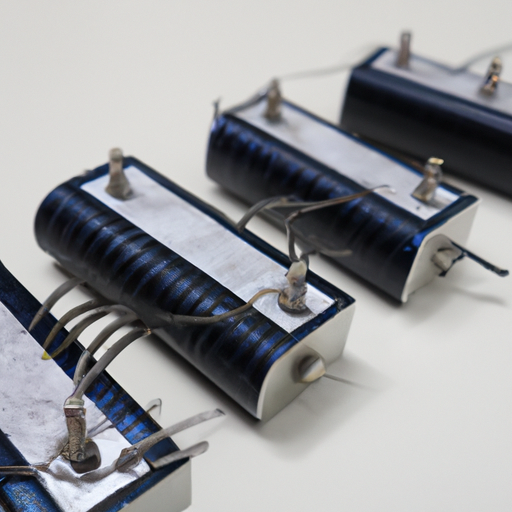
I. Introduction
Wirewound resistors are a type of resistor that is constructed by winding a metal wire around a core, typically made of ceramic or another insulating material. These resistors are known for their high precision, stability, and ability to handle high power levels, making them essential components in various electronic applications, from consumer electronics to industrial machinery. Understanding the production process of wirewound resistors is crucial for manufacturers and engineers alike, as it ensures the quality and reliability of these components. This blog post will delve into the materials, design specifications, production techniques, quality control measures, and future trends in the wirewound resistor industry.
II. Materials Used in Wirewound Resistors
A. Types of Wire Materials
The choice of wire material is critical in determining the performance characteristics of wirewound resistors. The most commonly used materials include:
1. **Nickel-chromium (NiCr)**: This alloy is favored for its excellent temperature stability and resistance to oxidation, making it suitable for high-temperature applications.
2. **Copper-nickel (CuNi)**: Known for its good conductivity and lower cost, CuNi is often used in applications where high precision is not as critical.
3. **Other alloys**: Various other alloys may be used depending on specific requirements, including resistance to corrosion and thermal stability.
B. Insulating Materials
Insulation is vital to prevent short circuits and ensure the resistor functions correctly. Common insulating materials include:
1. **Ceramic substrates**: These are often used for their high thermal stability and electrical insulation properties.
2. **Epoxy resins**: These materials provide good insulation and are often used in conjunction with ceramic substrates for added durability.
C. Coating Materials
Coatings serve both protective and functional purposes:
1. **Protective coatings**: These coatings protect the resistor from environmental factors such as moisture and dust.
2. **Color coding for identification**: Resistors are often color-coded to indicate their resistance values and tolerances, which is essential for easy identification during assembly and maintenance.
III. Design and Specifications
A. Determining Resistance Values
The resistance value of a wirewound resistor is determined by the length, cross-sectional area, and resistivity of the wire used. Engineers must carefully calculate these parameters to meet specific application requirements.
B. Power Rating Considerations
Power rating is a critical specification that indicates how much power a resistor can dissipate without overheating. This is influenced by the wire material, size, and insulation used.
C. Tolerance Levels
Tolerance levels indicate how much the actual resistance can vary from the specified value. High-precision applications may require resistors with tighter tolerances.
D. Size and Form Factor
The physical size and shape of the resistor are also important, as they must fit within the design constraints of the electronic device in which they will be used.
IV. The Production Process
A. Wire Preparation
1. **Wire drawing and annealing**: The production process begins with wire drawing, where metal is pulled through a die to achieve the desired diameter. Annealing follows to relieve stress and improve ductility.
2. **Cutting to specified lengths**: Once the wire is prepared, it is cut to the lengths required for the specific resistor design.
B. Winding the Wire
1. **Manual vs. automated winding**: Depending on the production scale, wire can be wound manually or using automated machines. Automated winding is more common in large-scale production due to its efficiency and consistency.
2. **Types of winding techniques**: Various winding techniques, such as helical or layered winding, can be employed based on the desired resistance and power rating.
C. Insulation Application
1. **Insulating the wire**: After winding, the wire is insulated to prevent electrical shorts. This can involve applying a thin layer of insulating material directly onto the wire.
2. **Application of ceramic or epoxy coatings**: The wound resistor is then coated with ceramic or epoxy to provide additional insulation and protection.
D. Sintering and Curing
1. **Sintering process for ceramic substrates**: If ceramic substrates are used, they undergo a sintering process where they are heated to a temperature that allows the particles to fuse together, enhancing their strength and insulating properties.
2. **Curing of epoxy coatings**: Epoxy coatings are cured through a chemical reaction that hardens the material, providing a durable protective layer.
E. Trimming and Testing
1. **Trimming to achieve precise resistance values**: After curing, the resistors are trimmed to achieve the exact resistance values specified in the design.
2. **Electrical testing for quality assurance**: Each resistor undergoes rigorous electrical testing to ensure it meets the required specifications and tolerances.
V. Quality Control Measures
A. In-process Inspections
Throughout the production process, in-process inspections are conducted to identify any defects or deviations from specifications. This includes checking wire diameter, winding consistency, and insulation integrity.
B. Final Testing Procedures
Once production is complete, final testing procedures are implemented to verify the performance of each resistor. This includes measuring resistance, power rating, and tolerance levels.
C. Compliance with Industry Standards
Manufacturers must ensure that their products comply with industry standards such as ISO and RoHS, which govern quality and environmental safety.
VI. Packaging and Distribution
A. Packaging Methods
Wirewound resistors are packaged in a manner that protects them during transportation and storage. This may involve anti-static bags, bubble wrap, or custom packaging solutions.
B. Labeling and Documentation
Each package is labeled with essential information, including resistance values, tolerances, and manufacturer details. Documentation may also include test results and compliance certifications.
C. Distribution Channels
Resistors are distributed through various channels, including direct sales to manufacturers, electronic component distributors, and online marketplaces.
VII. Challenges in Wirewound Resistor Production
A. Material Sourcing and Cost Fluctuations
The cost and availability of raw materials can fluctuate due to market conditions, impacting production costs and timelines.
B. Technological Advancements and Automation
While automation improves efficiency, it also requires manufacturers to invest in new technologies and training for their workforce.
C. Environmental Considerations and Sustainability
Manufacturers are increasingly focused on sustainability, seeking ways to reduce waste and energy consumption in the production process.
VIII. Future Trends in Wirewound Resistor Production
A. Innovations in Materials and Design
Research into new materials and designs is ongoing, with the aim of improving performance and reducing costs. This includes exploring alternative alloys and advanced insulation techniques.
B. Impact of Digitalization and Industry 4.0
The integration of digital technologies and Industry 4.0 principles is transforming production processes, enabling real-time monitoring and data analysis to enhance efficiency and quality.
C. Market Demand and Evolving Applications
As technology advances, the demand for high-precision wirewound resistors is expected to grow, particularly in sectors such as automotive, telecommunications, and renewable energy.
IX. Conclusion
The production process of wirewound resistors is a complex and meticulous endeavor that requires careful consideration of materials, design specifications, and quality control measures. As the demand for high-quality electronic components continues to rise, manufacturers must adapt to new challenges and embrace innovations to remain competitive. The future of the wirewound resistor industry looks promising, with advancements in materials and technology paving the way for enhanced performance and sustainability.
X. References
- Academic journals on electronic components and materials science.
- Industry reports on resistor manufacturing trends and market analysis.
- Manufacturer guidelines and specifications for wirewound resistors.
This comprehensive overview of the wirewound resistor production process highlights the intricacies involved in creating these essential electronic components, emphasizing the importance of quality and precision in manufacturing.