Latest Manufacturing Processes for Parallel Capacitors
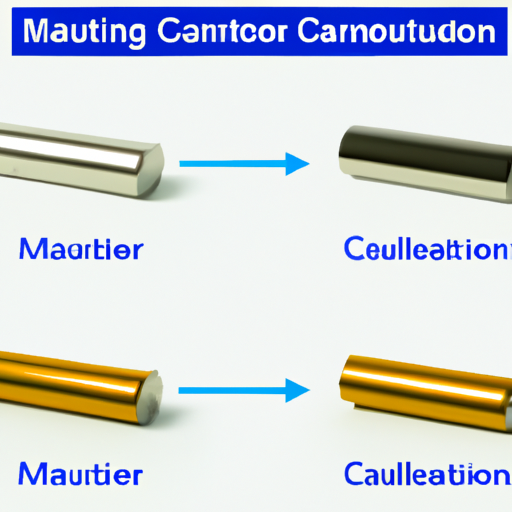
I. Introduction
Parallel capacitors are essential components in electronic circuits, serving to store and release electrical energy. They play a crucial role in filtering, timing, and energy storage applications, making them indispensable in various devices, from smartphones to industrial machinery. As technology advances, the manufacturing processes for these capacitors have evolved significantly, leading to improved performance, efficiency, and sustainability. This article explores the latest manufacturing processes for parallel capacitors, highlighting key techniques, materials, and future trends.
II. Historical Context
The manufacturing of capacitors has undergone a remarkable transformation over the decades. Initially, capacitors were made using simple materials like paper and aluminum foil, which limited their performance and application. Traditional methods focused on bulk production, often sacrificing quality for quantity. However, with the advent of modern technology, manufacturers have adopted advanced techniques that enhance capacitor design and functionality.
The introduction of new materials and fabrication methods has allowed for the miniaturization of capacitors, enabling their integration into smaller electronic devices. This evolution has not only improved the performance of capacitors but has also expanded their applications across various industries.
III. Types of Parallel Capacitors
Parallel capacitors come in several types, each with unique characteristics and applications:
A. Ceramic Capacitors
Ceramic capacitors are widely used due to their stability and reliability. They are made from ceramic materials and are ideal for high-frequency applications.
B. Electrolytic Capacitors
Electrolytic capacitors are known for their high capacitance values and are commonly used in power supply circuits. They are polarized, meaning they must be connected in the correct direction.
C. Film Capacitors
Film capacitors utilize thin plastic films as dielectrics. They offer excellent stability and low losses, making them suitable for audio and high-frequency applications.
D. Tantalum Capacitors
Tantalum capacitors are known for their high capacitance in a small size. They are often used in applications where space is limited, such as in mobile devices.
E. Comparison of Different Types
Each type of capacitor has its advantages and disadvantages, making them suitable for specific applications. Understanding these differences is crucial for selecting the right capacitor for a given circuit.
IV. Key Manufacturing Processes
The manufacturing of parallel capacitors involves several key processes, each critical to ensuring the quality and performance of the final product.
A. Material Selection
The choice of materials is fundamental in capacitor manufacturing.
1. **Dielectric Materials**: The dielectric material determines the capacitor's performance characteristics. Common dielectrics include ceramic, polyester, and tantalum oxide, each offering different properties such as temperature stability and voltage ratings.
2. **Conductive Materials**: Conductive materials, such as aluminum and copper, are used for the electrodes. The choice of conductive material affects the capacitor's efficiency and overall performance.
B. Fabrication Techniques
The fabrication of capacitors involves various techniques:
1. **Thin-Film Deposition**: This technique involves depositing thin layers of dielectric and conductive materials onto a substrate. It allows for precise control over the thickness and uniformity of the layers, resulting in high-performance capacitors.
2. **Thick-Film Printing**: Thick-film printing is used to create capacitors with larger dimensions. This method involves printing conductive pastes onto a substrate, which are then fired to create solid layers.
3. **Coating and Laminating**: Coating involves applying a protective layer over the capacitor, while laminating involves stacking multiple layers of materials to create a multi-layer capacitor. Both processes enhance the durability and performance of the capacitors.
C. Assembly Processes
The assembly of capacitors is a critical step in the manufacturing process:
1. **Layer Stacking**: In multi-layer capacitors, layers of dielectric and conductive materials are stacked to achieve the desired capacitance. This process requires precision to ensure uniformity and performance.
2. **Soldering Techniques**: Soldering is used to connect the capacitor to the circuit board. Advanced soldering techniques, such as reflow soldering, ensure strong and reliable connections.
3. **Encapsulation Methods**: Encapsulation protects capacitors from environmental factors. Various methods, including potting and molding, are used to ensure the longevity and reliability of the capacitors.
V. Advanced Manufacturing Technologies
The integration of advanced technologies has revolutionized capacitor manufacturing, leading to increased efficiency and performance.
A. Automation and Robotics
Automation plays a significant role in enhancing production efficiency.
1. **Role of Automation in Production Efficiency**: Automated systems streamline the manufacturing process, reducing human error and increasing output.
2. **Robotics in Assembly and Quality Control**: Robotics are increasingly used in assembly lines for tasks such as soldering and quality inspection, ensuring consistent quality and reducing production time.
B. Additive Manufacturing
Additive manufacturing, or 3D printing, is emerging as a game-changer in capacitor production.
1. **3D Printing of Capacitor Components**: This technology allows for the rapid prototyping of capacitor components, enabling manufacturers to test designs quickly and efficiently.
2. **Benefits and Challenges**: While additive manufacturing offers flexibility and customization, challenges such as material limitations and production speed must be addressed.
C. Nanotechnology
Nanotechnology is making significant strides in capacitor design.
1. **Use of Nanomaterials in Capacitor Design**: Incorporating nanomaterials can enhance the performance of capacitors, allowing for smaller sizes and higher capacitance.
2. **Impact on Performance and Size**: The use of nanotechnology can lead to capacitors that are not only more efficient but also occupy less space, making them ideal for modern electronic devices.
VI. Quality Control and Testing
Quality control is paramount in capacitor manufacturing to ensure reliability and performance.
A. Importance of Quality Assurance in Capacitor Manufacturing
Quality assurance processes help identify defects and ensure that capacitors meet industry standards.
B. Testing Methods
Various testing methods are employed to assess capacitor performance:
1. **Electrical Testing**: This includes measuring capacitance, leakage current, and equivalent series resistance (ESR) to ensure the capacitor meets specifications.
2. **Environmental Testing**: Capacitors are subjected to environmental conditions, such as temperature and humidity, to assess their reliability under different operating conditions.
3. **Reliability Testing**: Long-term reliability tests help predict the lifespan of capacitors, ensuring they perform well over time.
C. Standards and Certifications
Manufacturers must adhere to industry standards and certifications, such as ISO and RoHS, to ensure product quality and safety.
VII. Environmental Considerations
As the electronics industry grows, so does the need for sustainable manufacturing practices.
A. Sustainable Manufacturing Practices
Manufacturers are increasingly adopting eco-friendly practices, such as reducing waste and using recyclable materials.
B. Recycling and Disposal of Capacitors
Proper recycling and disposal methods are essential to minimize environmental impact. Many manufacturers are developing programs to recycle old capacitors and recover valuable materials.
C. Regulatory Compliance
Compliance with environmental regulations is crucial for manufacturers to avoid penalties and promote sustainability.
VIII. Future Trends in Capacitor Manufacturing
The future of capacitor manufacturing is bright, with several trends on the horizon.
A. Innovations on the Horizon
Emerging technologies, such as advanced materials and manufacturing techniques, promise to enhance capacitor performance and efficiency.
B. Market Demand and Technological Advancements
As electronic devices become more compact and powerful, the demand for high-performance capacitors will continue to grow, driving innovation in manufacturing processes.
C. Potential Challenges and Opportunities
While opportunities abound, challenges such as material shortages and regulatory compliance will require manufacturers to adapt and innovate continually.
IX. Conclusion
In summary, the manufacturing processes for parallel capacitors have evolved significantly, driven by advancements in technology and materials. Understanding these processes is essential for manufacturers and engineers alike, as they navigate the complexities of modern electronics. Staying updated with the latest trends and innovations will be crucial for ensuring the continued success and reliability of parallel capacitors in the ever-evolving landscape of electronic devices.
X. References
A comprehensive list of academic journals, industry reports, manufacturer guidelines, and online resources can provide further insights into the latest manufacturing processes for parallel capacitors. These resources are invaluable for anyone looking to deepen their understanding of this critical component in electronic circuits.
Latest Manufacturing Processes for Parallel Capacitors
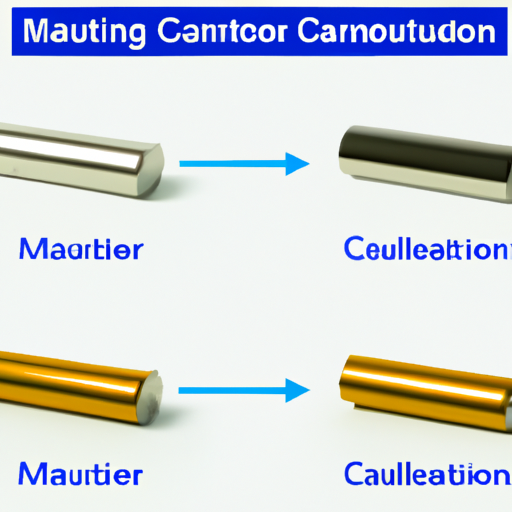
I. Introduction
Parallel capacitors are essential components in electronic circuits, serving to store and release electrical energy. They play a crucial role in filtering, timing, and energy storage applications, making them indispensable in various devices, from smartphones to industrial machinery. As technology advances, the manufacturing processes for these capacitors have evolved significantly, leading to improved performance, efficiency, and sustainability. This article explores the latest manufacturing processes for parallel capacitors, highlighting key techniques, materials, and future trends.
II. Historical Context
The manufacturing of capacitors has undergone a remarkable transformation over the decades. Initially, capacitors were made using simple materials like paper and aluminum foil, which limited their performance and application. Traditional methods focused on bulk production, often sacrificing quality for quantity. However, with the advent of modern technology, manufacturers have adopted advanced techniques that enhance capacitor design and functionality.
The introduction of new materials and fabrication methods has allowed for the miniaturization of capacitors, enabling their integration into smaller electronic devices. This evolution has not only improved the performance of capacitors but has also expanded their applications across various industries.
III. Types of Parallel Capacitors
Parallel capacitors come in several types, each with unique characteristics and applications:
A. Ceramic Capacitors
Ceramic capacitors are widely used due to their stability and reliability. They are made from ceramic materials and are ideal for high-frequency applications.
B. Electrolytic Capacitors
Electrolytic capacitors are known for their high capacitance values and are commonly used in power supply circuits. They are polarized, meaning they must be connected in the correct direction.
C. Film Capacitors
Film capacitors utilize thin plastic films as dielectrics. They offer excellent stability and low losses, making them suitable for audio and high-frequency applications.
D. Tantalum Capacitors
Tantalum capacitors are known for their high capacitance in a small size. They are often used in applications where space is limited, such as in mobile devices.
E. Comparison of Different Types
Each type of capacitor has its advantages and disadvantages, making them suitable for specific applications. Understanding these differences is crucial for selecting the right capacitor for a given circuit.
IV. Key Manufacturing Processes
The manufacturing of parallel capacitors involves several key processes, each critical to ensuring the quality and performance of the final product.
A. Material Selection
The choice of materials is fundamental in capacitor manufacturing.
1. **Dielectric Materials**: The dielectric material determines the capacitor's performance characteristics. Common dielectrics include ceramic, polyester, and tantalum oxide, each offering different properties such as temperature stability and voltage ratings.
2. **Conductive Materials**: Conductive materials, such as aluminum and copper, are used for the electrodes. The choice of conductive material affects the capacitor's efficiency and overall performance.
B. Fabrication Techniques
The fabrication of capacitors involves various techniques:
1. **Thin-Film Deposition**: This technique involves depositing thin layers of dielectric and conductive materials onto a substrate. It allows for precise control over the thickness and uniformity of the layers, resulting in high-performance capacitors.
2. **Thick-Film Printing**: Thick-film printing is used to create capacitors with larger dimensions. This method involves printing conductive pastes onto a substrate, which are then fired to create solid layers.
3. **Coating and Laminating**: Coating involves applying a protective layer over the capacitor, while laminating involves stacking multiple layers of materials to create a multi-layer capacitor. Both processes enhance the durability and performance of the capacitors.
C. Assembly Processes
The assembly of capacitors is a critical step in the manufacturing process:
1. **Layer Stacking**: In multi-layer capacitors, layers of dielectric and conductive materials are stacked to achieve the desired capacitance. This process requires precision to ensure uniformity and performance.
2. **Soldering Techniques**: Soldering is used to connect the capacitor to the circuit board. Advanced soldering techniques, such as reflow soldering, ensure strong and reliable connections.
3. **Encapsulation Methods**: Encapsulation protects capacitors from environmental factors. Various methods, including potting and molding, are used to ensure the longevity and reliability of the capacitors.
V. Advanced Manufacturing Technologies
The integration of advanced technologies has revolutionized capacitor manufacturing, leading to increased efficiency and performance.
A. Automation and Robotics
Automation plays a significant role in enhancing production efficiency.
1. **Role of Automation in Production Efficiency**: Automated systems streamline the manufacturing process, reducing human error and increasing output.
2. **Robotics in Assembly and Quality Control**: Robotics are increasingly used in assembly lines for tasks such as soldering and quality inspection, ensuring consistent quality and reducing production time.
B. Additive Manufacturing
Additive manufacturing, or 3D printing, is emerging as a game-changer in capacitor production.
1. **3D Printing of Capacitor Components**: This technology allows for the rapid prototyping of capacitor components, enabling manufacturers to test designs quickly and efficiently.
2. **Benefits and Challenges**: While additive manufacturing offers flexibility and customization, challenges such as material limitations and production speed must be addressed.
C. Nanotechnology
Nanotechnology is making significant strides in capacitor design.
1. **Use of Nanomaterials in Capacitor Design**: Incorporating nanomaterials can enhance the performance of capacitors, allowing for smaller sizes and higher capacitance.
2. **Impact on Performance and Size**: The use of nanotechnology can lead to capacitors that are not only more efficient but also occupy less space, making them ideal for modern electronic devices.
VI. Quality Control and Testing
Quality control is paramount in capacitor manufacturing to ensure reliability and performance.
A. Importance of Quality Assurance in Capacitor Manufacturing
Quality assurance processes help identify defects and ensure that capacitors meet industry standards.
B. Testing Methods
Various testing methods are employed to assess capacitor performance:
1. **Electrical Testing**: This includes measuring capacitance, leakage current, and equivalent series resistance (ESR) to ensure the capacitor meets specifications.
2. **Environmental Testing**: Capacitors are subjected to environmental conditions, such as temperature and humidity, to assess their reliability under different operating conditions.
3. **Reliability Testing**: Long-term reliability tests help predict the lifespan of capacitors, ensuring they perform well over time.
C. Standards and Certifications
Manufacturers must adhere to industry standards and certifications, such as ISO and RoHS, to ensure product quality and safety.
VII. Environmental Considerations
As the electronics industry grows, so does the need for sustainable manufacturing practices.
A. Sustainable Manufacturing Practices
Manufacturers are increasingly adopting eco-friendly practices, such as reducing waste and using recyclable materials.
B. Recycling and Disposal of Capacitors
Proper recycling and disposal methods are essential to minimize environmental impact. Many manufacturers are developing programs to recycle old capacitors and recover valuable materials.
C. Regulatory Compliance
Compliance with environmental regulations is crucial for manufacturers to avoid penalties and promote sustainability.
VIII. Future Trends in Capacitor Manufacturing
The future of capacitor manufacturing is bright, with several trends on the horizon.
A. Innovations on the Horizon
Emerging technologies, such as advanced materials and manufacturing techniques, promise to enhance capacitor performance and efficiency.
B. Market Demand and Technological Advancements
As electronic devices become more compact and powerful, the demand for high-performance capacitors will continue to grow, driving innovation in manufacturing processes.
C. Potential Challenges and Opportunities
While opportunities abound, challenges such as material shortages and regulatory compliance will require manufacturers to adapt and innovate continually.
IX. Conclusion
In summary, the manufacturing processes for parallel capacitors have evolved significantly, driven by advancements in technology and materials. Understanding these processes is essential for manufacturers and engineers alike, as they navigate the complexities of modern electronics. Staying updated with the latest trends and innovations will be crucial for ensuring the continued success and reliability of parallel capacitors in the ever-evolving landscape of electronic devices.
X. References
A comprehensive list of academic journals, industry reports, manufacturer guidelines, and online resources can provide further insights into the latest manufacturing processes for parallel capacitors. These resources are invaluable for anyone looking to deepen their understanding of this critical component in electronic circuits.