The Production Process of Mainstream Power Wire-Winding Resistors
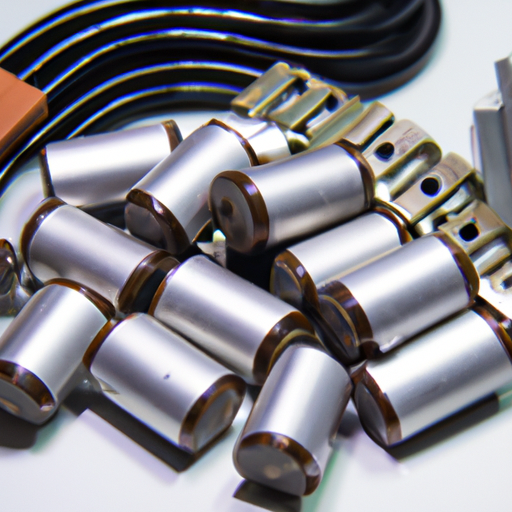
I. Introduction
Power wire-winding resistors are essential components in electrical and electronic applications, serving a critical role in managing current flow and dissipating heat. These resistors are designed to handle high power levels, making them indispensable in various industries, including automotive, telecommunications, and industrial machinery. Understanding the production process of these resistors not only sheds light on their functionality but also highlights the intricate engineering and materials science involved in their creation.
II. Understanding Power Wire-Winding Resistors
A. Basic Principles of Operation
Power wire-winding resistors operate on the principle of resistance, which is the opposition to the flow of electric current. When current passes through a resistor, electrical energy is converted into heat, which must be managed to prevent damage to the component and surrounding circuitry. The ability to dissipate heat effectively is a key characteristic of power wire-winding resistors, allowing them to maintain performance under high-load conditions.
B. Types of Wire-Winding Resistors
There are several types of wire-winding resistors, each designed for specific applications:
1. **Fixed Resistors**: These resistors have a predetermined resistance value and are commonly used in circuits where stable performance is required.
2. **Variable Resistors**: Also known as potentiometers, these allow for adjustable resistance, making them useful in applications like volume controls and tuning circuits.
3. **Specialty Resistors**: These include precision resistors and those designed for specific environmental conditions, such as high-temperature or high-voltage applications.
III. Materials Used in Production
A. Conductive Materials
The choice of materials is crucial in the production of power wire-winding resistors. The most common conductive materials include:
1. **Types of Wire**: Copper is widely used due to its excellent conductivity, while nickel-chromium alloys are favored for their high-temperature resistance and stability.
2. **Insulating Materials**: Insulation is vital to prevent short circuits and ensure safety. Common insulating materials include enamel coatings and ceramic insulators, which can withstand high temperatures.
B. Components for Housing and Mounting
The housing and mounting components of wire-winding resistors are equally important. They provide structural integrity and thermal management.
1. **Ceramic and Metal Housings**: Ceramic housings are preferred for their heat resistance, while metal housings offer durability and effective heat dissipation.
2. **Heat Sinks and Thermal Management Materials**: These components help to dissipate heat generated during operation, ensuring the resistor functions within safe temperature limits.
IV. The Production Process
A. Design and Engineering
The production of power wire-winding resistors begins with design and engineering. This phase involves:
1. **Specifications and Requirements**: Engineers define the electrical and thermal specifications based on the intended application, including resistance values, power ratings, and environmental conditions.
2. **Prototyping and Testing**: Initial prototypes are created and subjected to rigorous testing to ensure they meet the required specifications. This step is crucial for identifying potential issues before mass production.
B. Wire Preparation
Once the design is finalized, the next step is wire preparation:
1. **Selection of Wire Gauge and Material**: The appropriate wire gauge is selected based on the desired resistance and power rating. Thicker wires can handle more current but may also generate more heat.
2. **Cutting and Prepping the Wire**: The wire is cut to the required lengths and prepped for winding, which may involve stripping insulation from the ends.
C. Winding Process
The winding process is a critical step in the production of wire-winding resistors:
1. **Manual vs. Automated Winding Techniques**: Depending on the scale of production, winding can be done manually or through automated machines. Automated winding offers precision and consistency, while manual winding may be used for custom or low-volume orders.
2. **Winding Patterns and Configurations**: The wire is wound around a core in specific patterns to achieve the desired resistance and heat dissipation characteristics. The configuration can vary based on the resistor type and application.
D. Insulation Application
After winding, insulation is applied to protect the wire and enhance safety:
1. **Types of Insulation**: Common insulation types include enamel coatings, which provide a thin, durable layer, and thicker coatings for added protection.
2. **Application Techniques**: Insulation can be applied through various methods, including dipping the wound resistor in a liquid insulation material or spraying it on for even coverage.
E. Assembly and Housing
The assembly phase involves securing the wound wire in its housing:
1. **Mounting the Wound Wire**: The insulated wire is carefully mounted within its housing, ensuring that it is securely positioned to prevent movement during operation.
2. **Securing the Resistor in its Housing**: The housing is sealed, often using adhesives or mechanical fasteners, to protect the internal components from environmental factors.
F. Testing and Quality Control
Quality control is paramount in the production of power wire-winding resistors:
1. **Electrical Testing**: Each resistor undergoes electrical testing to verify its resistance value and tolerance. This ensures that it meets the specified performance criteria.
2. **Thermal Testing**: Thermal testing assesses the resistor's ability to dissipate heat under load conditions, ensuring it operates safely within its thermal limits.
3. **Final Inspection and Certification**: A final inspection is conducted to check for any defects or inconsistencies. Once approved, the resistors are certified for use in their intended applications.
V. Challenges in Production
The production of power wire-winding resistors is not without its challenges:
A. Material Sourcing and Cost Fluctuations
The availability and cost of raw materials can fluctuate, impacting production costs and timelines. Manufacturers must navigate these challenges to maintain profitability while ensuring quality.
B. Precision in Manufacturing
Achieving precision in the winding process and insulation application is critical. Even minor deviations can affect the performance and reliability of the resistors.
C. Meeting Industry Standards and Regulations
Manufacturers must comply with various industry standards and regulations, which can vary by region and application. Staying updated on these requirements is essential for market competitiveness.
VI. Innovations and Future Trends
The production of power wire-winding resistors is evolving, driven by innovations and trends in technology:
A. Advances in Materials Science
Research into new materials is leading to the development of resistors with improved performance characteristics, such as higher thermal resistance and lower weight.
B. Automation and Smart Manufacturing
The integration of automation and smart manufacturing techniques is enhancing production efficiency and precision, allowing for greater scalability and reduced labor costs.
C. Environmental Considerations and Sustainability
As industries move towards sustainability, manufacturers are exploring eco-friendly materials and processes to reduce their environmental impact. This includes recycling initiatives and the use of biodegradable materials.
VII. Conclusion
The production process of mainstream power wire-winding resistors is a complex interplay of engineering, materials science, and manufacturing precision. From the initial design phase to the final testing and certification, each step is crucial in ensuring the reliability and performance of these essential components. As technology continues to advance, the role of power wire-winding resistors in modern applications will only grow, paving the way for innovations that enhance their functionality and sustainability.
VIII. References
- Academic Journals
- Industry Reports
- Manufacturer Guidelines and Standards
This comprehensive overview of the production process of power wire-winding resistors highlights their significance in various applications and the intricate steps involved in their creation. As the industry evolves, staying informed about advancements and trends will be essential for manufacturers and users alike.
The Production Process of Mainstream Power Wire-Winding Resistors
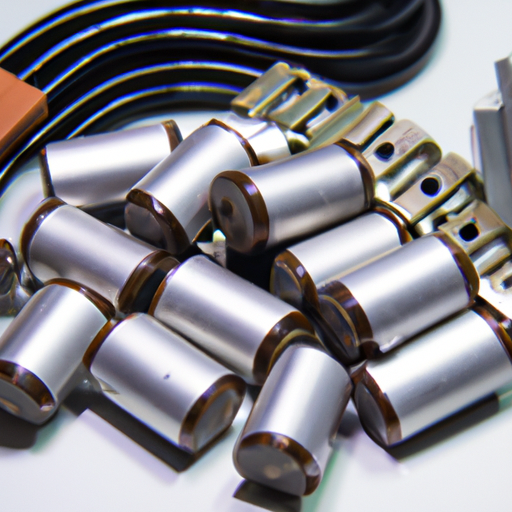
I. Introduction
Power wire-winding resistors are essential components in electrical and electronic applications, serving a critical role in managing current flow and dissipating heat. These resistors are designed to handle high power levels, making them indispensable in various industries, including automotive, telecommunications, and industrial machinery. Understanding the production process of these resistors not only sheds light on their functionality but also highlights the intricate engineering and materials science involved in their creation.
II. Understanding Power Wire-Winding Resistors
A. Basic Principles of Operation
Power wire-winding resistors operate on the principle of resistance, which is the opposition to the flow of electric current. When current passes through a resistor, electrical energy is converted into heat, which must be managed to prevent damage to the component and surrounding circuitry. The ability to dissipate heat effectively is a key characteristic of power wire-winding resistors, allowing them to maintain performance under high-load conditions.
B. Types of Wire-Winding Resistors
There are several types of wire-winding resistors, each designed for specific applications:
1. **Fixed Resistors**: These resistors have a predetermined resistance value and are commonly used in circuits where stable performance is required.
2. **Variable Resistors**: Also known as potentiometers, these allow for adjustable resistance, making them useful in applications like volume controls and tuning circuits.
3. **Specialty Resistors**: These include precision resistors and those designed for specific environmental conditions, such as high-temperature or high-voltage applications.
III. Materials Used in Production
A. Conductive Materials
The choice of materials is crucial in the production of power wire-winding resistors. The most common conductive materials include:
1. **Types of Wire**: Copper is widely used due to its excellent conductivity, while nickel-chromium alloys are favored for their high-temperature resistance and stability.
2. **Insulating Materials**: Insulation is vital to prevent short circuits and ensure safety. Common insulating materials include enamel coatings and ceramic insulators, which can withstand high temperatures.
B. Components for Housing and Mounting
The housing and mounting components of wire-winding resistors are equally important. They provide structural integrity and thermal management.
1. **Ceramic and Metal Housings**: Ceramic housings are preferred for their heat resistance, while metal housings offer durability and effective heat dissipation.
2. **Heat Sinks and Thermal Management Materials**: These components help to dissipate heat generated during operation, ensuring the resistor functions within safe temperature limits.
IV. The Production Process
A. Design and Engineering
The production of power wire-winding resistors begins with design and engineering. This phase involves:
1. **Specifications and Requirements**: Engineers define the electrical and thermal specifications based on the intended application, including resistance values, power ratings, and environmental conditions.
2. **Prototyping and Testing**: Initial prototypes are created and subjected to rigorous testing to ensure they meet the required specifications. This step is crucial for identifying potential issues before mass production.
B. Wire Preparation
Once the design is finalized, the next step is wire preparation:
1. **Selection of Wire Gauge and Material**: The appropriate wire gauge is selected based on the desired resistance and power rating. Thicker wires can handle more current but may also generate more heat.
2. **Cutting and Prepping the Wire**: The wire is cut to the required lengths and prepped for winding, which may involve stripping insulation from the ends.
C. Winding Process
The winding process is a critical step in the production of wire-winding resistors:
1. **Manual vs. Automated Winding Techniques**: Depending on the scale of production, winding can be done manually or through automated machines. Automated winding offers precision and consistency, while manual winding may be used for custom or low-volume orders.
2. **Winding Patterns and Configurations**: The wire is wound around a core in specific patterns to achieve the desired resistance and heat dissipation characteristics. The configuration can vary based on the resistor type and application.
D. Insulation Application
After winding, insulation is applied to protect the wire and enhance safety:
1. **Types of Insulation**: Common insulation types include enamel coatings, which provide a thin, durable layer, and thicker coatings for added protection.
2. **Application Techniques**: Insulation can be applied through various methods, including dipping the wound resistor in a liquid insulation material or spraying it on for even coverage.
E. Assembly and Housing
The assembly phase involves securing the wound wire in its housing:
1. **Mounting the Wound Wire**: The insulated wire is carefully mounted within its housing, ensuring that it is securely positioned to prevent movement during operation.
2. **Securing the Resistor in its Housing**: The housing is sealed, often using adhesives or mechanical fasteners, to protect the internal components from environmental factors.
F. Testing and Quality Control
Quality control is paramount in the production of power wire-winding resistors:
1. **Electrical Testing**: Each resistor undergoes electrical testing to verify its resistance value and tolerance. This ensures that it meets the specified performance criteria.
2. **Thermal Testing**: Thermal testing assesses the resistor's ability to dissipate heat under load conditions, ensuring it operates safely within its thermal limits.
3. **Final Inspection and Certification**: A final inspection is conducted to check for any defects or inconsistencies. Once approved, the resistors are certified for use in their intended applications.
V. Challenges in Production
The production of power wire-winding resistors is not without its challenges:
A. Material Sourcing and Cost Fluctuations
The availability and cost of raw materials can fluctuate, impacting production costs and timelines. Manufacturers must navigate these challenges to maintain profitability while ensuring quality.
B. Precision in Manufacturing
Achieving precision in the winding process and insulation application is critical. Even minor deviations can affect the performance and reliability of the resistors.
C. Meeting Industry Standards and Regulations
Manufacturers must comply with various industry standards and regulations, which can vary by region and application. Staying updated on these requirements is essential for market competitiveness.
VI. Innovations and Future Trends
The production of power wire-winding resistors is evolving, driven by innovations and trends in technology:
A. Advances in Materials Science
Research into new materials is leading to the development of resistors with improved performance characteristics, such as higher thermal resistance and lower weight.
B. Automation and Smart Manufacturing
The integration of automation and smart manufacturing techniques is enhancing production efficiency and precision, allowing for greater scalability and reduced labor costs.
C. Environmental Considerations and Sustainability
As industries move towards sustainability, manufacturers are exploring eco-friendly materials and processes to reduce their environmental impact. This includes recycling initiatives and the use of biodegradable materials.
VII. Conclusion
The production process of mainstream power wire-winding resistors is a complex interplay of engineering, materials science, and manufacturing precision. From the initial design phase to the final testing and certification, each step is crucial in ensuring the reliability and performance of these essential components. As technology continues to advance, the role of power wire-winding resistors in modern applications will only grow, paving the way for innovations that enhance their functionality and sustainability.
VIII. References
- Academic Journals
- Industry Reports
- Manufacturer Guidelines and Standards
This comprehensive overview of the production process of power wire-winding resistors highlights their significance in various applications and the intricate steps involved in their creation. As the industry evolves, staying informed about advancements and trends will be essential for manufacturers and users alike.