What is the Mainstream Resistor Diagram Production Process?
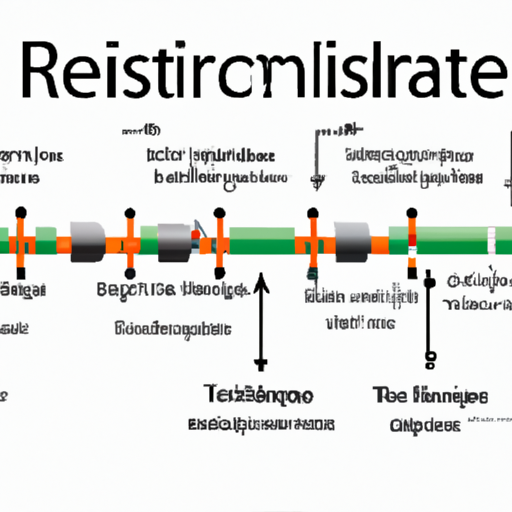
I. Introduction
A. Definition of Resistors
Resistors are fundamental components in electronic circuits, designed to limit the flow of electric current. They are characterized by their resistance value, measured in ohms (Ω), and play a crucial role in controlling voltage and current levels within a circuit. Resistors can be found in various forms, including fixed, variable, and specialty types, each serving specific functions in electronic applications.
B. Importance of Resistor Diagrams in Electronics
Resistor diagrams, also known as circuit diagrams or schematics, are essential for visualizing and understanding electronic circuits. They provide a graphical representation of the components and their interconnections, allowing engineers and technicians to design, analyze, and troubleshoot circuits effectively. A well-drafted resistor diagram can significantly enhance communication among team members and facilitate the manufacturing process.
C. Overview of the Production Process
The production of resistor diagrams involves several stages, from initial design to finalization. This process requires a combination of creativity, technical knowledge, and proficiency in specialized software tools. In this blog post, we will explore the various steps involved in creating resistor diagrams, the quality control measures in place, the challenges faced, and the future trends shaping this field.
II. Understanding Resistor Diagrams
A. Components of a Resistor Diagram
1. Symbol Representation
In resistor diagrams, components are represented by standardized symbols. For instance, a resistor is typically depicted as a zigzag line or a rectangle, depending on the schematic style. Understanding these symbols is crucial for interpreting diagrams accurately.
2. Circuit Context
The context in which resistors are used is equally important. Resistor diagrams often include other components such as capacitors, inductors, and power sources, providing a comprehensive view of the circuit's functionality.
B. Types of Resistor Diagrams
1. Schematic Diagrams
Schematic diagrams are abstract representations of electrical circuits, focusing on the connections and relationships between components rather than their physical layout. These diagrams are invaluable for circuit design and analysis, as they simplify complex circuits into understandable formats.
2. Layout Diagrams
Layout diagrams, on the other hand, provide a physical representation of how components are arranged on a printed circuit board (PCB). These diagrams are crucial for manufacturing and assembly, ensuring that components are placed correctly to maintain circuit integrity.
C. Applications of Resistor Diagrams in Circuit Design
Resistor diagrams are used in various applications, including consumer electronics, automotive systems, and industrial machinery. They serve as blueprints for engineers, guiding the design process and ensuring that circuits function as intended.
III. The Production Process of Resistor Diagrams
A. Initial Design Phase
1. Conceptualization
The production of a resistor diagram begins with conceptualization. Engineers and designers brainstorm ideas, considering the circuit's purpose and the specific requirements of the project. This phase often involves collaboration among team members to ensure that all aspects of the design are considered.
2. Software Tools Used (e.g., CAD software)
Once the initial concept is established, designers turn to computer-aided design (CAD) software to create the diagram. Popular tools include Eagle, Altium Designer, and KiCAD, which offer features tailored for electronic design automation (EDA). These tools allow for precise placement of components and easy modifications.
B. Component Selection
1. Types of Resistors (e.g., carbon, metal film, wire-wound)
Selecting the appropriate type of resistor is critical to the circuit's performance. Designers must consider factors such as resistance value, power rating, and temperature coefficient. Common types include carbon film, metal film, and wire-wound resistors, each with unique characteristics suited for different applications.
2. Specifications and Tolerances
In addition to type, specifications such as tolerance (the allowable deviation from the stated resistance value) and power rating (the maximum power the resistor can dissipate) must be carefully chosen to ensure reliability and performance.
C. Drafting the Diagram
1. Creating the Schematic
With components selected, the next step is drafting the schematic. Designers use their CAD software to place symbols representing resistors and other components, connecting them with lines that represent electrical connections. This stage requires attention to detail to ensure accuracy.
2. Incorporating Circuit Elements
As the schematic develops, designers incorporate additional circuit elements, such as power sources, capacitors, and switches. Each element must be placed logically to reflect the intended functionality of the circuit.
D. Review and Revision
1. Peer Review Process
Once the initial draft is complete, it undergoes a peer review process. Colleagues examine the diagram for errors, omissions, and potential improvements. This collaborative approach helps identify issues that may have been overlooked.
2. Iterative Improvements
Based on feedback, designers make iterative improvements to the diagram. This may involve adjusting component placements, refining connections, or even re-evaluating component choices to enhance circuit performance.
E. Finalization
1. Exporting the Diagram
After revisions are complete, the final diagram is exported in various formats, such as PDF or SVG, for documentation and sharing. This ensures that the design is accessible to all stakeholders involved in the project.
2. Documentation and Annotation
Proper documentation is essential for clarity and future reference. Designers annotate the diagram with relevant information, such as component values, part numbers, and notes on circuit functionality. This documentation aids in troubleshooting and future modifications.
IV. Quality Control in Resistor Diagram Production
A. Standards and Regulations
1. Industry Standards (e.g., IPC, IEEE)
Quality control is a critical aspect of resistor diagram production. Adhering to industry standards, such as those set by the Institute of Printed Circuits (IPC) and the Institute of Electrical and Electronics Engineers (IEEE), ensures that diagrams meet established criteria for accuracy and reliability.
2. Compliance Checks
Compliance checks are conducted throughout the production process to verify that the diagram aligns with these standards. This may involve reviewing the schematic against a checklist of requirements or conducting simulations to validate circuit behavior.
B. Testing and Validation
1. Simulation Tools
Before finalizing a design, engineers often use simulation tools to test the circuit's performance virtually. Software such as SPICE allows designers to analyze how the circuit will behave under various conditions, identifying potential issues before physical implementation.
2. Real-world Testing
Once the circuit is built, real-world testing is conducted to validate the design. This step is crucial for ensuring that the resistor diagram accurately represents the intended functionality and that the circuit operates as expected.
V. Challenges in Resistor Diagram Production
A. Complexity of Modern Circuits
As technology advances, circuits become increasingly complex, posing challenges for designers. Managing numerous components and connections can lead to errors, making it essential to maintain clarity and organization in resistor diagrams.
B. Evolving Technology and Tools
The rapid evolution of design tools and technologies requires designers to stay updated on the latest software and methodologies. This constant change can be overwhelming, necessitating ongoing education and training.
C. Ensuring Accuracy and Clarity
Maintaining accuracy and clarity in resistor diagrams is paramount. Misrepresentations can lead to circuit failures, making it essential for designers to double-check their work and adhere to best practices.
VI. Future Trends in Resistor Diagram Production
A. Automation and AI in Design
The future of resistor diagram production is likely to see increased automation and the integration of artificial intelligence (AI) in design processes. AI can assist in optimizing circuit layouts, suggesting component selections, and even identifying potential issues before they arise.
B. Integration with Other Design Processes
As electronic design becomes more interconnected, resistor diagrams will increasingly integrate with other design processes, such as mechanical design and software development. This holistic approach will enhance collaboration and streamline the overall design workflow.
C. Enhanced Visualization Techniques
Advancements in visualization techniques, such as 3D modeling and augmented reality, will provide designers with new ways to interact with and understand resistor diagrams. These tools can enhance comprehension and facilitate better communication among team members.
VII. Conclusion
A. Recap of the Importance of Resistor Diagrams
Resistor diagrams are vital tools in the field of electronics, providing a clear representation of circuit designs and facilitating effective communication among engineers and technicians. Their importance cannot be overstated, as they serve as the foundation for successful circuit implementation.
B. Summary of the Production Process
The production process of resistor diagrams involves several key stages, including initial design, component selection, drafting, review, and finalization. Each step is crucial for ensuring the accuracy and reliability of the final product.
C. Final Thoughts on the Future of Resistor Diagram Production
As technology continues to evolve, the production of resistor diagrams will adapt to meet new challenges and opportunities. Embracing automation, AI, and enhanced visualization techniques will pave the way for more efficient and effective design processes, ultimately leading to better electronic products.
VIII. References
A. Academic Journals
- IEEE Transactions on Circuits and Systems
- Journal of Electronic Materials
B. Industry Standards Documentation
- IPC-2221: Generic Standard on Printed Board Design
- IEEE 315: Standard Graphic Symbols for Electrical and Electronics Diagrams
C. Relevant Books and Articles on Circuit Design and Resistors
- "The Art of Electronics" by Paul Horowitz and Winfield Hill
- "Electronic Principles" by Albert Malvino and David Bates
This comprehensive overview of the mainstream resistor diagram production process highlights the importance of these diagrams in electronics, the steps involved in their creation, and the future trends that will shape their development. Understanding this process is essential for anyone involved in electronic design and engineering.
What is the Mainstream Resistor Diagram Production Process?
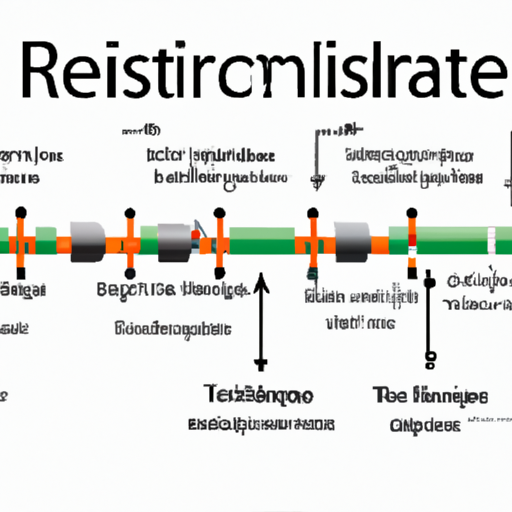
I. Introduction
A. Definition of Resistors
Resistors are fundamental components in electronic circuits, designed to limit the flow of electric current. They are characterized by their resistance value, measured in ohms (Ω), and play a crucial role in controlling voltage and current levels within a circuit. Resistors can be found in various forms, including fixed, variable, and specialty types, each serving specific functions in electronic applications.
B. Importance of Resistor Diagrams in Electronics
Resistor diagrams, also known as circuit diagrams or schematics, are essential for visualizing and understanding electronic circuits. They provide a graphical representation of the components and their interconnections, allowing engineers and technicians to design, analyze, and troubleshoot circuits effectively. A well-drafted resistor diagram can significantly enhance communication among team members and facilitate the manufacturing process.
C. Overview of the Production Process
The production of resistor diagrams involves several stages, from initial design to finalization. This process requires a combination of creativity, technical knowledge, and proficiency in specialized software tools. In this blog post, we will explore the various steps involved in creating resistor diagrams, the quality control measures in place, the challenges faced, and the future trends shaping this field.
II. Understanding Resistor Diagrams
A. Components of a Resistor Diagram
1. Symbol Representation
In resistor diagrams, components are represented by standardized symbols. For instance, a resistor is typically depicted as a zigzag line or a rectangle, depending on the schematic style. Understanding these symbols is crucial for interpreting diagrams accurately.
2. Circuit Context
The context in which resistors are used is equally important. Resistor diagrams often include other components such as capacitors, inductors, and power sources, providing a comprehensive view of the circuit's functionality.
B. Types of Resistor Diagrams
1. Schematic Diagrams
Schematic diagrams are abstract representations of electrical circuits, focusing on the connections and relationships between components rather than their physical layout. These diagrams are invaluable for circuit design and analysis, as they simplify complex circuits into understandable formats.
2. Layout Diagrams
Layout diagrams, on the other hand, provide a physical representation of how components are arranged on a printed circuit board (PCB). These diagrams are crucial for manufacturing and assembly, ensuring that components are placed correctly to maintain circuit integrity.
C. Applications of Resistor Diagrams in Circuit Design
Resistor diagrams are used in various applications, including consumer electronics, automotive systems, and industrial machinery. They serve as blueprints for engineers, guiding the design process and ensuring that circuits function as intended.
III. The Production Process of Resistor Diagrams
A. Initial Design Phase
1. Conceptualization
The production of a resistor diagram begins with conceptualization. Engineers and designers brainstorm ideas, considering the circuit's purpose and the specific requirements of the project. This phase often involves collaboration among team members to ensure that all aspects of the design are considered.
2. Software Tools Used (e.g., CAD software)
Once the initial concept is established, designers turn to computer-aided design (CAD) software to create the diagram. Popular tools include Eagle, Altium Designer, and KiCAD, which offer features tailored for electronic design automation (EDA). These tools allow for precise placement of components and easy modifications.
B. Component Selection
1. Types of Resistors (e.g., carbon, metal film, wire-wound)
Selecting the appropriate type of resistor is critical to the circuit's performance. Designers must consider factors such as resistance value, power rating, and temperature coefficient. Common types include carbon film, metal film, and wire-wound resistors, each with unique characteristics suited for different applications.
2. Specifications and Tolerances
In addition to type, specifications such as tolerance (the allowable deviation from the stated resistance value) and power rating (the maximum power the resistor can dissipate) must be carefully chosen to ensure reliability and performance.
C. Drafting the Diagram
1. Creating the Schematic
With components selected, the next step is drafting the schematic. Designers use their CAD software to place symbols representing resistors and other components, connecting them with lines that represent electrical connections. This stage requires attention to detail to ensure accuracy.
2. Incorporating Circuit Elements
As the schematic develops, designers incorporate additional circuit elements, such as power sources, capacitors, and switches. Each element must be placed logically to reflect the intended functionality of the circuit.
D. Review and Revision
1. Peer Review Process
Once the initial draft is complete, it undergoes a peer review process. Colleagues examine the diagram for errors, omissions, and potential improvements. This collaborative approach helps identify issues that may have been overlooked.
2. Iterative Improvements
Based on feedback, designers make iterative improvements to the diagram. This may involve adjusting component placements, refining connections, or even re-evaluating component choices to enhance circuit performance.
E. Finalization
1. Exporting the Diagram
After revisions are complete, the final diagram is exported in various formats, such as PDF or SVG, for documentation and sharing. This ensures that the design is accessible to all stakeholders involved in the project.
2. Documentation and Annotation
Proper documentation is essential for clarity and future reference. Designers annotate the diagram with relevant information, such as component values, part numbers, and notes on circuit functionality. This documentation aids in troubleshooting and future modifications.
IV. Quality Control in Resistor Diagram Production
A. Standards and Regulations
1. Industry Standards (e.g., IPC, IEEE)
Quality control is a critical aspect of resistor diagram production. Adhering to industry standards, such as those set by the Institute of Printed Circuits (IPC) and the Institute of Electrical and Electronics Engineers (IEEE), ensures that diagrams meet established criteria for accuracy and reliability.
2. Compliance Checks
Compliance checks are conducted throughout the production process to verify that the diagram aligns with these standards. This may involve reviewing the schematic against a checklist of requirements or conducting simulations to validate circuit behavior.
B. Testing and Validation
1. Simulation Tools
Before finalizing a design, engineers often use simulation tools to test the circuit's performance virtually. Software such as SPICE allows designers to analyze how the circuit will behave under various conditions, identifying potential issues before physical implementation.
2. Real-world Testing
Once the circuit is built, real-world testing is conducted to validate the design. This step is crucial for ensuring that the resistor diagram accurately represents the intended functionality and that the circuit operates as expected.
V. Challenges in Resistor Diagram Production
A. Complexity of Modern Circuits
As technology advances, circuits become increasingly complex, posing challenges for designers. Managing numerous components and connections can lead to errors, making it essential to maintain clarity and organization in resistor diagrams.
B. Evolving Technology and Tools
The rapid evolution of design tools and technologies requires designers to stay updated on the latest software and methodologies. This constant change can be overwhelming, necessitating ongoing education and training.
C. Ensuring Accuracy and Clarity
Maintaining accuracy and clarity in resistor diagrams is paramount. Misrepresentations can lead to circuit failures, making it essential for designers to double-check their work and adhere to best practices.
VI. Future Trends in Resistor Diagram Production
A. Automation and AI in Design
The future of resistor diagram production is likely to see increased automation and the integration of artificial intelligence (AI) in design processes. AI can assist in optimizing circuit layouts, suggesting component selections, and even identifying potential issues before they arise.
B. Integration with Other Design Processes
As electronic design becomes more interconnected, resistor diagrams will increasingly integrate with other design processes, such as mechanical design and software development. This holistic approach will enhance collaboration and streamline the overall design workflow.
C. Enhanced Visualization Techniques
Advancements in visualization techniques, such as 3D modeling and augmented reality, will provide designers with new ways to interact with and understand resistor diagrams. These tools can enhance comprehension and facilitate better communication among team members.
VII. Conclusion
A. Recap of the Importance of Resistor Diagrams
Resistor diagrams are vital tools in the field of electronics, providing a clear representation of circuit designs and facilitating effective communication among engineers and technicians. Their importance cannot be overstated, as they serve as the foundation for successful circuit implementation.
B. Summary of the Production Process
The production process of resistor diagrams involves several key stages, including initial design, component selection, drafting, review, and finalization. Each step is crucial for ensuring the accuracy and reliability of the final product.
C. Final Thoughts on the Future of Resistor Diagram Production
As technology continues to evolve, the production of resistor diagrams will adapt to meet new challenges and opportunities. Embracing automation, AI, and enhanced visualization techniques will pave the way for more efficient and effective design processes, ultimately leading to better electronic products.
VIII. References
A. Academic Journals
- IEEE Transactions on Circuits and Systems
- Journal of Electronic Materials
B. Industry Standards Documentation
- IPC-2221: Generic Standard on Printed Board Design
- IEEE 315: Standard Graphic Symbols for Electrical and Electronics Diagrams
C. Relevant Books and Articles on Circuit Design and Resistors
- "The Art of Electronics" by Paul Horowitz and Winfield Hill
- "Electronic Principles" by Albert Malvino and David Bates
This comprehensive overview of the mainstream resistor diagram production process highlights the importance of these diagrams in electronics, the steps involved in their creation, and the future trends that will shape their development. Understanding this process is essential for anyone involved in electronic design and engineering.